1.在每一權(quán)通句硫化機地溝支管道的閥門前端增加1個緩沖罐
緩沖罐罐體材料可選用Y108mX10mm的厚壁無縫鋼管,罐憶長200 mn, 兩端焊5 um厚的鋼板。硫化排水時,尚速水流首先沖擊緩沖罐壁,打在罐上向四周飛濺,在緩沖罐上部飛濺幾次勸能消耗后落在緩沖罐底部,在重力的作用下,緩緩流向地溝支答。這樣即把原先沖刷地溝文管的高速水流轉(zhuǎn)移到緩沖端上。這種緩沖錘成木較低,至少可用3-4年,H易于更換,即只要關閉單臺殖化機進地溝支管的閥門,拆卸螺栓, 10~20 min就可以換好。
2.調(diào)整硫化熱水回收時間
采用緩沖后出從根本上解決了動力水排術,抽真空排水、總并管排水高道水流對地溝支管的戶刷問題,但解決不了冷卻水排水高速水流對地溝支管的沖刷問題。在T.1.-B1320/2895X2雙模硫化機排水管道上安裝緩沖罐后的試驗過程中,我們發(fā)現(xiàn)在輪胎能化程序熱水回收結(jié)京后進冷卻水時,前1分多鐘排出的冷卻水仍然以高連流沖刷著地溝支管,而1分多鐘后才變成緩緩的水流,經(jīng)分析后認為是二次蒸汽造成的。在輪胎硫化程序中有一個熱水回收租序,收置這個熱水回收程序的目的是將硫化咬囊中的170~190"C熱水回收到熱水除氧裝置的補水罐中,以節(jié)省能源。然而,無論硫化工藝采用的是燕汽推熱水。還是直接采用冷卻水推熱水,一般都不能將膠囊中的熱水回收干凈,況且膠囊本身還帶有很大熱量。因此,在熱水回收程序結(jié)束后,冷卻水進入膠囊后很快義升溫;變成120~ 140C的熱水,在熱水從冷卻水排水管排向硫化機地溝支管的過程中,其壓力從約2, 0MPa降至常壓,這必然要產(chǎn)生二次蒸發(fā),形成蒸汽。查《石油化工裝置工藝管道安裝設計手冊》可知,當熱水壓力從2.0 MPa降至常壓時,每千克熱水可產(chǎn)生0.22 kg左右的蒸汽;查《機械工廠節(jié)能設計及使用手冊》可知,120一140C熱水對應的飽和蒸汽的壓力為0.20~ 0.35MPa(絕壓)。
為了進一步弄清由二次蒸發(fā)引起的汽液混合高速流,在LL- B1320/2895X2雙模硫化機冷卻水回管道上裝上壓力表.(見圖8)又做了-項試驗。當冷卻水循環(huán)剛開始時,1#緩沖罐壓力表顯示0.2MPa(表壓),2#緩沖罐壓力表顯示0.07MPa(表壓),此時排水口水流速度仍很高。經(jīng)過約70s后,兩壓力表顯示慢慢都回到零,同時排水口水流趨于平緩。:根據(jù)這項試驗,我們調(diào)整了確化工藝,將LL-B1320/2895X2雙模硫化機熱水回收的時間由1 min改為2 min, 這樣使得冷卻水循環(huán)的初始溫度由調(diào)整前的140C降到100C左右,由于排水溫度降低了,二次蒸發(fā)造成的蒸汽量大為減小,因此冷卻水經(jīng)過1個緩沖罐后,水流的動能基木耗盡,緩沖罐主水口不再出現(xiàn)消急的水流。據(jù)此,我們分別對其它幾種型號雙模硫化機的熱水回收時間進行了調(diào)整
3.增設倒U形彎頭
在雙模硫化機冷卻水、動力水、抽真空排水、總排水的回水管道中增設1個倒u形彎頭倒U形彎頭的管頂最高點高于地溝支回水管最末端的管頂高度,其日的是使地溝支回水管始終充滿水,同時也不影響管路系統(tǒng)正常的重力回水運行方式。因為緩沖罐到地溝支回水管的高度差為1m左右,即使回水的動能在緩沖罐中消耗完,在重力的作用下,回水從截面1流到截面2時仍形成一一個流速,根據(jù)《供暖通風設計手冊》可計算出截面2處的最小流速:v2=4.47 m●s'
通過上述改善措施,取得了成效,在延長硫化管道使用壽命的同時,由于調(diào)整了硫化熱水回收時間,使熱能損耗得以減少。以LL-B1320/2895X2雙模硫化機為例:與原硫化工藝相比,改進后每次可多回收平均溫度為120C的熱水93.4 kg,每天硫化22次,可減少熱量損失6.07X105kJ,折合壓力為1. 5MPa的蒸汽217 kg, 以每噸蒸汽為80元計算,折合17. 36元,一年運行300天,1臺雙模硫化機一年僅靠增加熱水回收量一項就可使生產(chǎn)成本減少5 208元。如果再加上節(jié)省的管道維修費用和增加的開機率,實施這3種改普硫化管道的措施后節(jié)省的費用更為可觀。
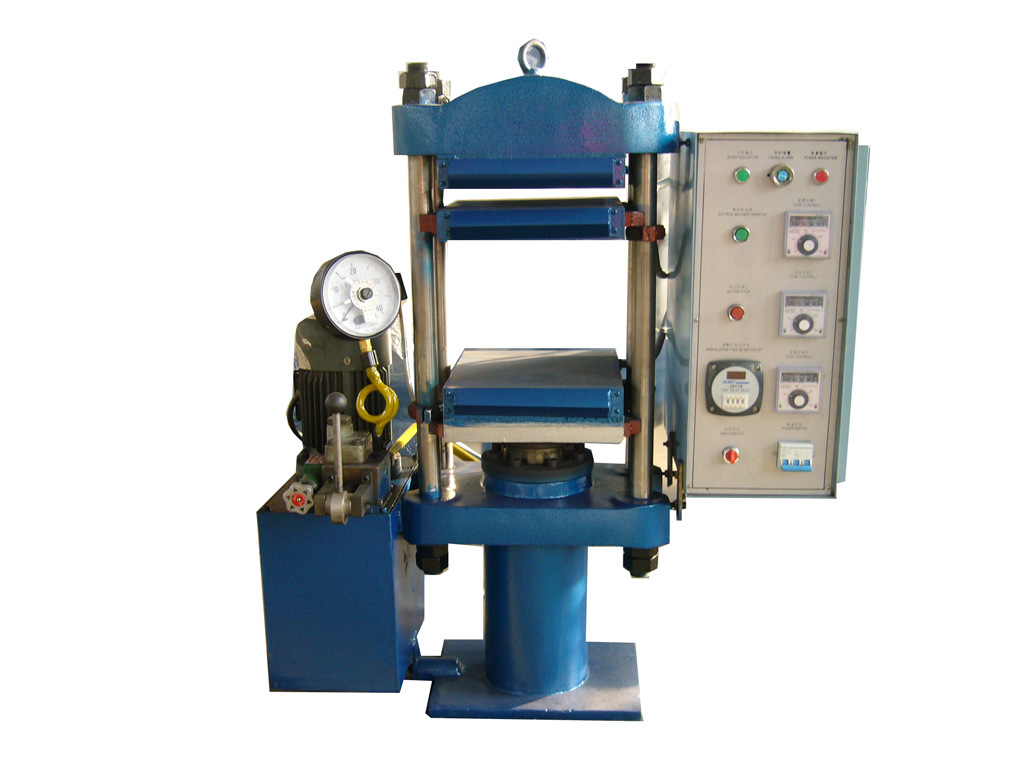